This article was originally posted on PinballRehab.com.
Reproduced with permission from terryb.
Written by terryb

A. Basic Soldering Tutorial
B. Basic Desoldering Tutorial
– Supplies Needed
C. Tools for Advanced Soldering
D. Advanced Soldering Tutorial
E. Advanced Desoldering Tutorial
This is part five of a five part series on soldering. This article is specifically oriented towards the advanced soldering techniques. It covers the techniques necessary to desolder circuit board components.
The most important things to know about desoldering is that it is much harder than soldering and is where most of the circuit board damage occurs (lifted traces or pads, destroyed through-holes, etc.). The sad part is that all of this is avoidable if you respect the board and know what you’re doing.
Should I be Repairing Circuit Boards?
Only you can answer this question, but consider that board repair shops have reported the number of hacked (non-repairable) boards has increased dramatically since Clay put out his repair guides. Just as you wouldn’t buy a pair of hair clippers, decide you’re a hairdresser and cut your wife’s hair, the same is true of soldering.
Moving from soldering a diode onto a solenoid to doing board work requires a quantum leap in equipment, knowledge and experience. This article will provide the knowledge, but you will still need quality equipment and plenty of practice. If you’re not willing to make that commitment then just send the board our for repair.
In addition, if you can’t read a schematic well enough to test a circuit with a DMM after desoldering you should not be doing board repair.
In Image 3 you can see the result of amateur repair work done on a Williams CPU. When I got the board, the switch matrix circuit would only work when I pressed down on the IC in question. Once I got the chip off I found the previous “repair person” had destroyed 7 pads/through-holes and four traces. Although pretty amazing, this is not at all uncommon.
Circuit Boards
Most circuit boards since 1980 use through-hole technology. This allows traces to be located on both sides of the board and when conductivity is needed from one side of the board to the other a through-hole is used (see image to the right). When a connection to a component is only needed on one side of the board, a pad is used rather than a through-hole.
The through-hole, or pad, is actually one physical part and the board trace a second physical part. They are electrically connected once the board is wave-soldered. It is not uncommon for the connection to break right at the point where the through-hole, or pad, is soldered to the board trace. It is also not uncommon (especially after someone has hacked the board) to find a pad destroyed or the metal liner in the through-hole damaged.
Desoldering Tools and Supplies
The Basic Desoldering Tutorial covers solder wick, desoldering pump (often called a solder sucker), flux and other basic desoldering tools in detail, which I will not repeat here.
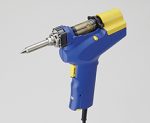
One tool I will mention is the Hakko 808 Desoldering Gun. If you’re going to do much circuit board desoldering this is a worthwhile investment. I’ve used rework stations that cost thousands of dollars and did not do as good a job as the Hakko.
[Editors note: The Hakko 808 Desoldering Gun is no longer manufactured. Used ones are available. It’s replacement is the Hakko FR301.]
The tip on the Hakko is oval with a hole in the middle for the vacuum. You place the tip over the lead for a couple of seconds and when the solder melts, wiggle the tip back and forth while pulling the trigger for the vacuum pump. One shot will typically get all of the solder out and the wiggling motion prevents the lead from maintaining a bond with side of the land (see excerpt from manual to the right).
If you purchase the Hakko product, also get the 1.6mm tip and cleaning tool in addition to the 1.0mm tip it comes with. You will need this for doing large connector pins, transistors and other components with larger leads.
I really can’t say enough about this product and it is the only way, if used properly, to guarantee that you will never lift a pad or trace. I speak from experience, and I’ve been soldering professionally for almost 30 years.
One other product I should mention is the [ECG J-045-DS Electric Corded De-Soldering Iron]. It has a bulb attached to the iron form removing solder as you work. While it might seem like a good idea, the tip temperature of a 45 Watt iron is approximately 788 degrees which is way to hot to be used safely on a circuit board.
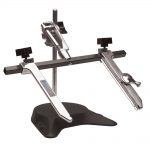
Note: It does not require any more temperature to desolder than to solder (650 – 700 degrees).
If you’re going to use solder wick or a solder sucker you will also need a clamp, or vise, to hold the board so you can work from both sides at the same time. The Panavise 333 is a good solution, and then add a longer crossbar so you can hold CPU boards.
Of course, you could put the $50 towards a Hakko, and you won’t need a clamp. See the references for an article on desoldering tools, including the Hakko [desoldering iron].
Preparation
Unless you’re using a desoldering gun, the first step is to clip all of the leads from the component (IC, transistor, resistor, etc.) and get it out of the way. I seriously don’t know why people skip this step. It only takes a few seconds and if you’re trying to save a 20 year-old IC for reuse (in case it’s not bad I guess, which is another beef of mine), to be blunt, you’re a fool.
Get a good pair of side-cutters that are made specifically for working on electronics . The tip is narrower than the standard variety side cutters. allowing you to reach between IC pins and clip the leads.
More than anything else, this step will minimize your chance of damaging a board. Not only will it be easier to desolder the component, but you won’t be tempted to pry the component loose while its leads are still attached to a pad or through-hole.
I saw a video of someone trying to remove a bridge rectifier without cutting it away from the board first. After desoldering he then used a 12″ screwdriver to pry the component off. To no ones surprise, except his own, he lifted the circuit pad and about two inches of trace.
Note: Use a Dremel tool with a cutter blade to remove bridge rectifiers.
If you are using a soldering iron, always size the soldering iron tip to the job: .0625″ for IC’s and small transistors, .125″ for larger (driver) transistors and .187″ for bridge rectifiers.
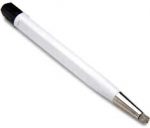
The next step is to mechanically clean the solder joints with a fiberglass pen. Joints should be nice and shiny when you’re done.
At this point you want to add a little flux to all of the joints. I hear a lot of people say if you’re having trouble desoldering to add a little solder and then try again. The benefit of that advice is that you’re adding flux to the joint, so just skip the solder and add the flux.
Desoldering
I will specifically be talking about removing an IC, but the same theory applies to other components. I will cover using the Hakko in the attached video and will talk here about using a solder sucker. If you want to use solder wick instead that’s fine, the same procedure works.
Using your clamp, orient the board so you are looking at one of the edges and you can reach both sides of the board. Grasp the component side of the lead with a pair of needle-nose pliers and place your soldering iron on the joint on the opposite side. The iron should be at about a 30 degree angle to the board and as the solder melts do not press the iron down onto the circuit pad.
Just keep heating (should only take a couple of seconds) until the lead easily pulls out. Continue until all of the leads are removed.
Now place your soldering iron on one side of the board and the solder sucker on the other side. Heat the joint until the solder melts and trigger your solder sucker. You may have to repeat from the other side to get a good clean land. Solder wick also works good for cleanup.
An alternative technique is to use a solder sucker from the component side of the board to remove the pin and solder at the same time.
Any vacuum type device requires a minimum solder mass before it will work effectively. If you’re down to that last little bit of solder and having trouble either add a tiny amount of solder or use a solder wick.
Note: The ground pin on an IC will always be the hardest to desolder because the larger trace draws heat away from the joint.
If you are having trouble desoldering a joint do not increase the soldering iron temperature above 700 degrees or use longer dwell times (more than a few seconds). Instead try cleaning the joint physically and/or adding a little more flux.
You can clean up any holes by using a toothpick while applying heat. Once done, clean the area with flux remover (flux turns acidic when heated).
Note: If you’re using solder wick instead of a sucker, place the wick across the land then then put your soldering iron on top of the wick. Use a chisel tip and lay the soldering iron over at a 10 – 20 degree angle from the board to maximize contact between the iron and the wick. Always add flux to either the solder wick or the joint to improve performance. Liquid flux works well if you’re adding the flux to the solder wick.
Hakko Desoldering Tool
With the Hakko you can skip cutting the leads from the IC. See note below.
The main thing is to keep the tip from touching the circuit board. If you have trouble with this slide the end of a toothpick under the tip as the solder melts. This is especially important because the Hakko runs slightly hotter than what is normally recommended for desoldering (the reason they get away with this is because it works so quickly, remember temperature management is more important than temperature).
If the pitch of the vacuum changes while desoldering, you are most likely pressing the tip against the board, which restricts air flow and causes the change in sound.
There are five temperature selections ranging from 715 – 895 degrees. Hakko recommends using the 1 – 2 setting for single layer boards, 3 – 4 for through-hole boards and 5 for multilayer boards. Personally I use the 2 setting most of the time on pinball circuit boards.
Please note in the following video how a distance is maintained from the board. Although the rocking motion used to free the lead in the video is correct it is done for too long a period (six seconds, when only about 2-3 seconds is needed) and the vacuum is running constantly rather than just firing for a couple of seconds once the solder is liquid.
As soon as I place the tip on the joint I begin rocking it back and forth. It will move some since the inside diameter of the tip is larger than the lead. After 2-3 swings, the solder will melt and you can feel the tip moving in a larger arc. If you listen closely you will also hear a faint click when the lead releases. At this point, pull the trigger for a couple of seconds while you continue to wiggle the lead.
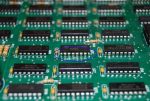
Turn the board over and on the component side make sure all pads are free of solder. See Image 4 where the right lead of the IC still has solder. If there is any remaining solder you can either add a little solder (on the non-component side of the board) and try again, or use the following technique.
Many people use a modified technique with the Hakko when removing IC’s. Desolder all pins as described, turn the board over and just clip any pins that still have solder in place. Remove the IC from the board and then pull any remaining pins by heating the joint with a soldering iron.
One of the pro tricks is to use a hot air rework station, or hot air rework gun (at home I use the Aoyue 8032++ Hand Held Digital Hot Air Rework Gun), to loosen up any remaining solder on the pins. First desolder the component as described above. Then with the board component side down, hit it with the hot air (700 degrees is a good temperature) and the chip will typically fall out of the board.
The Aoyue 8032++ also works great for re-flowing solder on connectors and components.
Removing the Component
This section applies if you are removing a component with all pins still attached .
A through-hole can look completely clean (remember to check from both sides of the board, especially the top) but still have a small amount of solder holding the lead to the side wall of the eyelet. You can test each of the leads by using a small screwdriver or a soldering pick with a slot in it. Just place it on each lead and make sure the lead moves easily from side to side.
If it doesn’t move freely, heat the joint until the solder melts and then while the solder is cooling, wiggle the lead from side to side with the pick until the solder hardens.
You should be able to easily pull the IC out using just your hand. Do not put a screwdriver under the IC and pry it out: you will lift pads and traces (this is the single most common reason for damaged pads and traces). It sometimes helps to grab the IC and twist it slightly (clockwise and counter-clockwise) to break loose any pins that are still adhering.
Inspection
Visually inspect all traces, pads and through-holes for any physical damage with a magnifier. It is not uncommon to get hairline cracks at the point where the pad or through-hole connects to the trace.
Always test any through-holes from one side of the board to the other to make sure there is conductivity. Damage to through-holes is not always visible and will keep solder from properly flowing from one side of the board to the other.
You want to be absolutely sure that all pads and through-holes are in good shape before continuing. Any damage will need to be repaired before installing the new component.
Practice, Practice, Practice
There is nothing that beats practice. The best way is to find an old non-working CPU board from a computer and practice desoldering and soldering components until you’re an expert. While a lot of people recommend learning on some type of electronics kit, anyone can solder together a bunch of brand new components and on a brand new board.
You are much better off working with an older board that will be more similar to the challenges provided by a twenty some year-old pinball circuit board.
[Editors note: TerryB’s video is not available. However, he has the following video reference in his files which covers similar information.]
Comments
Comments, including suggestions, improvements, errors, etc. are welcome (see below).
If you have a specific question about your game, please see our FAQ section.